Machine Lubrication and Pultrusion System
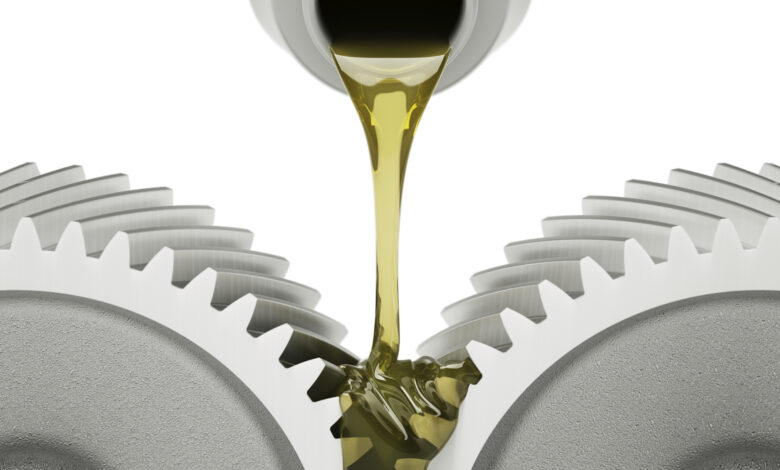
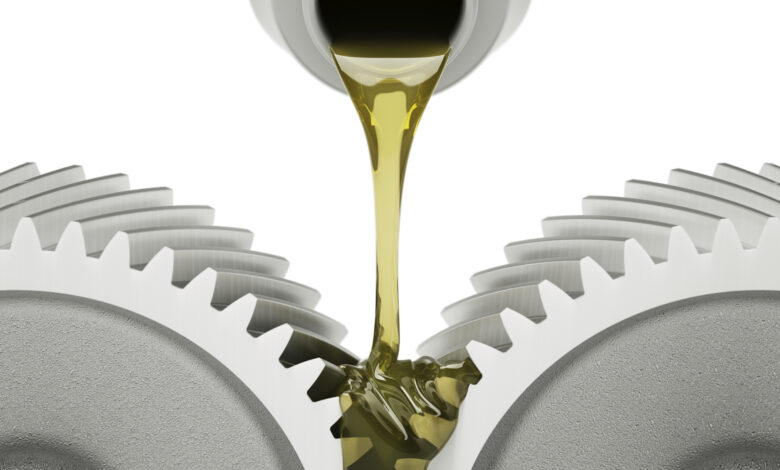
Introduction
https://isohitech.com/ Machine lubrication is a critical aspect of maintaining industrial equipment, ensuring smooth operation and longevity. When it comes to specific systems like pultrusion, where high temperatures and pressures are involved, effective lubrication becomes even more paramount.
Importance of Lubrication in Machinery
Enhancing Efficiency
Proper lubrication reduces friction between moving parts, enabling machinery to operate more efficiently. In pultrusion systems, where composite materials are processed, friction can cause overheating and damage if not adequately managed.
Preventing Wear and Tear
https://mikeshoppingroom.com/ Continuous friction can lead to premature wear and tear of components, resulting in costly repairs and downtime. Lubricants act as a protective barrier, preventing direct metal-to-metal contact and extending the lifespan of machinery.
Reducing Friction
Friction generates heat, which can adversely affect the quality of pultruded products. By reducing friction through lubrication, manufacturers can maintain consistent product quality and minimize defects.
Understanding Pultrusion Systems
Definition and Functionality
Pultrusion is a manufacturing process used to produce continuous lengths of composite materials with a constant cross-section. It involves pulling fiber reinforcements through a resin bath and into a heated die, where the materials cure and solidify.
Components of Pultrusion Systems
Pultrusion systems consist of various components, including pulling mechanisms, resin baths, heating zones, and cooling systems. Each component plays a crucial role in the pultrusion process and requires proper lubrication for optimal performance.
The Role of Lubrication in Pultrusion Systems
Ensuring Smooth Operation
Lubricants facilitate smooth movement of components within pultrusion systems, reducing friction and preventing mechanical failures. Proper lubrication ensures that pultrusion machinery operates reliably, producing high-quality products consistently.
Minimizing Maintenance Downtime
Regular lubrication maintenance helps prevent unexpected breakdowns and reduces downtime for repairs. By adhering to a proactive lubrication schedule, manufacturers can minimize production interruptions and maximize throughput.
Extending Equipment Lifespan
Effective lubrication extends the lifespan of pultrusion equipment by reducing wear on critical components. By investing in proper lubrication practices, manufacturers can protect their assets and avoid premature equipment replacement costs.
Types of Lubricants Used in Pultrusion Systems
Synthetic Lubricants
Synthetic lubricants offer superior temperature resistance and chemical stability, making them ideal for pultrusion applications. They provide long-lasting protection against friction and wear, even under extreme operating conditions.
Greases
https://incomepultrusion.com/ Greases are commonly used in pultrusion systems to lubricate bearings, gears, and other moving parts. They offer excellent adhesion and resistance to water washout, ensuring reliable lubrication in challenging environments.
Oil-Based Lubricants
Oil-based lubricants are versatile and widely used in pultrusion systems for their lubricating properties and compatibility with various materials. They come in different viscosities to suit different operating conditions and equipment requirements.
Best Practices for Lubricating Pultrusion Systems
Regular Maintenance Schedule
Implementing a regular maintenance schedule for lubrication ensures that pultrusion systems operate at peak efficiency and reliability. This includes routine inspections, lubricant replenishment, and monitoring of equipment condition.
Proper Lubrication Techniques
Applying lubricants correctly is essential for effective protection against friction and wear. Proper lubrication techniques include applying the right amount of lubricant, distributing it evenly, and following manufacturer recommendations.
Monitoring Lubricant Performance
Regularly monitoring lubricant performance helps detect issues such as contamination or degradation early on. By conducting oil analysis and equipment inspections, manufacturers can identify potential problems and take corrective action before they escalate.
Challenges in Lubricating Pultrusion Systems
High Temperatures and Pressure
Pultrusion systems operate at high temperatures and pressures, which can degrade lubricants and reduce their effectiveness. Selecting lubricants with high temperature resistance and thermal stability is crucial for maintaining performance under these conditions.
Compatibility Issues with Materials
Some lubricants may not be compatible with certain composite materials used in pultrusion, leading to product contamination or degradation. Manufacturers must carefully select lubricants that are compatible with their specific materials to avoid quality issues.
Environmental Considerations
Environmental factors such as exposure to moisture, dust, and chemicals can affect lubricant performance in pultrusion systems. Choosing lubricants with good environmental resistance helps ensure reliable operation and product quality in harsh conditions.
Innovations in Lubrication Technology for Pultrusion Systems
Self-Lubricating Materials
Advancements in material science have led to the development of self-lubricating materials that reduce the need for external lubrication. These materials contain embedded lubricants that are released during operation, providing continuous lubrication for moving parts.
Advanced Lubricant Formulations
Manufacturers are continually developing advanced lubricant formulations tailored to the unique requirements of pultrusion systems. These formulations offer improved performance, durability, and environmental compatibility, enhancing the efficiency and reliability of pultrusion processes.
Case Studies: Successful Implementation of Lubrication Strategies in Pultrusion Systems
Future Trends and Developments in Machine Lubrication for Pultrusion Systems
Conclusion
In conclusion, effective machine lubrication is essential for optimizing the performance and longevity of pultrusion systems. By understanding the importance of lubrication, selecting the right lubricants, and implementing best practices, manufacturers can ensure smooth operation, minimize maintenance downtime, and maximize equipment lifespan.